Vacuum Conveyors
Vacuum conveyor is used to transport dry powder and granular materials from point A to point B in a closed system (pneumatic transport line, e.g. pipe and hose).
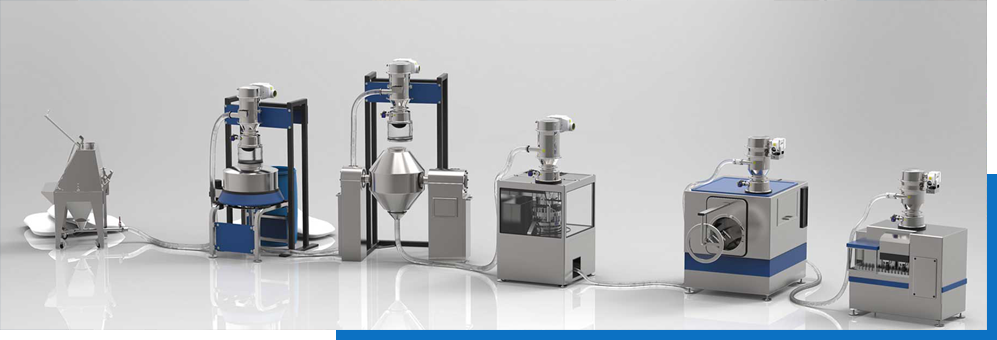
The production of food, pharmaceuticals and chemical materials requires the highest level of safety in terms of health compliance and operation. Piab’s vacuum conveyor models have been developed to ensure operational safety and health compliance in the food, pharmaceutical and chemical industries.
Piab conveyors are ATEX Dust certified. piFLOW®p and piFLOW®t are ATEX Gas certified. All conveyors are available with either an ejector driven vacuum pump or a mechanical pump.
Our goal is to provide our customers with solutions that will increase their productivity.
piFLOW®p SMART – Solution for Automatic Vacuum Conveying
piFLOW®p SMART is a stand-alone system with machine learning software and sophisticated algorithms that run the application to reach the maximum capacity for the conveyed material. To reach the maximum material capacity an air carrying unit is integrated in the system. If there is a vertical lift higher than 8 meters in the conveying pipeline, Piab is offering a pipeline emptying unit to prevent blockage of the pipeline. All the vacuum conveying functions are controlled by the electrical control unit ECU-15S and its software.
piFLOW®p – High Requirement Vacuum Conveying
The piFLOW®p product range is the most versatile, premium offering among the Piab vacuum conveyors. They are available with 2, 3, 7, 14, 33, and 56 l [0.07, 0.11, 0.25, 0.49, 1.17, and 1.98 ft³] batch sizes which can convey up to 15 tons/hour [30 000 lbs/h]. No matter the scale, a piFLOW®p can cover it across a wide range of applications throughout the food, pharmaceuticals, chemicals, and additive manufacturing industries. The piFLOW®p range is designed with an acid-resistant stainless-steel body (ASTM 316L), meets FDA, EC No. 1935/2004, and EU No. 10/2011 requirements. Depending on the configuration, piFLOW®p can be delivered with ATEX Gas, ATEX Dust, or both ATEX Gas and Dust certifications. The piFLOW®p conveys a vast array of solid materials, like powders, granules, and particles. Examples include nutraceuticals, excipients, metal powder, sugar, milk powder, powdered yeast, drink mixes, cheese powder, spice blends, resin, cocoa, toner, cereals, freeze-dried fruits, zirconia powder, xylitol, and many more… The piFLOW®p range takes care of conveying solid materials no matter the scale. The smaller vacuum conveyors in the piFLOW®p range are perfect for when a small amount of excipients need to be conveyed to a tablet press or cases where the conveyor has to work in a constrained space. The medium-sized vacuum conveyors are used to feed sieves in additive manufacturing or to fill or discharge drums/bags, mixers, etc. The highest capacity piFLOW®p vacuum conveyors are required when charging reactors, mixers, or filling/discharging big bags. The piFLOW®p range is available in four automation levels. The Standard version gives you all the reliable, essential functions of vacuum conveyors. The BVO or Batch Volume Optimisation features a level sensor, helping with the setup of the most critical parameter, the charge timer, making the setup and operation of the vacuum conveyor easier and safer. CCO or Conveyor Cycle Optimisation operates with two level sensors, optimising the entire batch, increasing the ease of use. With CCO only the carried air volume must be set manually. Auto-tuning is a fully automatic solution that optimises the full system setup for extremely reduced time on material changeovers. It eliminates the need for manual timer settings thanks to the two separate level sensors which let the Electrical Control Unit know when the vacuum conveyor is full and when it has been fully emptied. The pipeline Emptying Unit prevents any potential blockages in the pipelines, and the Air Carrying Unit even sets the carrying air to material ratio automatically. The system uses machine learning and automatically tunes itself, even taking environmental factors such as temperature and humidity into account, adjusting automatically as these fluctuate. Both CCO and Auto-tuning work in a system equipped with the ECU-15 electrical control unit, which saves the conveyed materials and recipes.
piFLOW®t – Gentle Vacuum Conveying
Our premium conveyors are designed with a Stainless Steel body (ASTM 316L) and meet the very high hygienic demands of FDA. Piab conveyors are ATEX Dust certified and piFLOW®t also has ATEX Gas certification. Typical applications are transfer of tablets, capsules, coffee, granules and other fragile products. Also hygienic applications or places where space is at a premium.
piFLOW®am – Additive Manufacturing Vacuum Conveying
piFLOWam was specially designed with challenges associated with metal powder management in mind. It can transfer metal powders with high bulk density while having a minimal footprint. It allows piFLOWam to fit on top of a 3D printer, an intermediate vessel or a depowdering station even in constrained spaces, overcoming the vertical lift to avoid climbing ladders and feeding the printer manually. By automating metal powder handling, operators save time, productivity increases, and production can take the next level in industrial automation. The piFLOWam features a stainless-steel body (ASTM 316L), a butterfly valve, and a standard TC-coupling for easy integration.
piFLOW®fc – Heavy Duty Vacuum Conveying
The piFLOW®fc product range is the recommended choice in the food and chemicals industries where the highest level of hygiene is required. They are available with 3, 7, 14, and 33 l [0.11, 0.25, 0.49, 1.17 ft³] batch sizes which can convey up to 8 tons/hour [16 000 lbs/h]. The piFLOW®fc range is designed with a stainless-steel body (ASTM 304L), meets FDA, EC No. 1935/2004, and EC No. 10/2011 requirements. The piFLOW®fc range has a high throughput while also ensuring a small footprint, dust-free operation, and reduced maintenance time. Typical applications include cocoa, cookie dough, crisps, and certain chemicals – the piFLOW®fc vacuum conveyor can handle it all. The piFLOW®fc range is available with two different levels of automation. The standard version delivers the basic functionality and reliability of the piFLOW®fc product range. The BVO or Batch Volume Optimisation features a level sensor, helping with the setup of the most critical parameter, the charge timer, making the setup and operation of the vacuum conveyor easier and safer.
piFLOW®f – Food Grade Vacuum Conveying
The piFLOW®f is our most popular vacuum conveyor in the food industry. It replaces manual handling or mechanical conveyors such as screw conveyors or bucket elevators to ensure a safer, ergonomic, dust-free working environment in food manufacturing facilities. Typical materials conveyed include a wide variety of powders and granules, including, but not limited to salt, flour, granulated or icing sugar, coffee (powder or whole beans), tea, protein powder or other functional food, oats, paprika powder, cocoa, dried goods (e.g. pasta), lentils, rice, seeds (hemp, peanuts, cashew, etc…), spices, bread crumbs, cheese powder, rice crisps, chickpeas, birdseed, pet food, fish oil capsules, dried fruits, and more. Piab has conducted a significant number of tests related to different food applications. The test results are a part of the Piab knowledge base, therefore, feasibility checks are provided within an extremely low timeframe in case of most requests. The piFLOW®f range consists of models with 6, 8, 14, and 28 l [0.21, 0.28, 0.49, 0.99 ft³] batch volumes, which can convey up to 7.5 tons/h [15 000 lbs/h]. They are designed with a stainless-steel body (ASTM 304L). All parts which are in contact with the conveyed materials (the conveyor body and sealings) are compliant with FDA, EC No. 1935/2004, and EC No. 10/2011. ATEX Dust certification is available, depending on the configuration. This range is available with two automation levels. The standard version is a straightforward, reliable vacuum conveyor. In contrast, the BVO or Batch Volume Optimisation version features a level sensor to facilitate batch volume setup, leading to a shorter amount of conveyor setup at material changeovers, and secure a higher level of operation safety by reducing the possibility of human error.
piFLOW®i – Industrial Vacuum Conveying
When there is a need for a more robust, reliable, versatile solution to convey industrial materials, piFLOW®i is the best choice. Typical materials conveyed include detergents, desiccants, sand, industrial salt, toner powder, clay, chromium oxide, aluminium oxide, talc, silica, cigarette filters, walnut shells, litter, PVC powder, plastic pellets, calcium carbonate, methylcellulose, alumina powder, or plastic pellets/parts, and many more… The piFLOW®i can replace mechanical conveyors such as bucket elevators or belt conveyors to ensure an ergonomic, dust-free working environment without respiratory risks for the operators, especially when hazardous, toxic, or allergenic materials are conveyed. The piFLOW®i range consists of models with 6, 8, 14, and 28 l [0.21, 0.28, 0.49, 0.99 ft³] batch volumes, which can convey up to 7.5 tons/h [15 000 lbs/h]. They are designed with a stainless-steel body (ASTM 304L). All parts which are in contact with the conveyed materials (the conveyor body and sealings) are compliant with EC no. 1935/2004, and EC No. 10/2011; ATEX Dust certification is available, depending on the configuration. This range is available with two different automation levels. The standard version which is a straightforward, reliable vacuum conveyor. In contrast, the BVO or Batch Volume Optimisation features a level sensor to facilitate batch volume setup, leading to a shorter amount of conveyor setup at material changeovers and secure a higher level of operation safety by reducing the possibility of human error.